5 Ways to Optimize Production Workflow Within Your Auto Body Shop
-
Written by David McCreight
-
Published on February 07, 2024
-
Category: Productivity and Efficiency
Optimizing production workflow within your auto body shop is the key to maximizing customer satisfaction and revenue. Using the latest technology and management practices, it is easier than ever to streamline the activities of your collision repair center. Keep reading to discover five ways to optimize your auto body shop’s production workflow.
1. Implement Lean Management System
Prioritizing the most important actions in any industry is a recipe for efficiency, and lean management systems are famous for "trimming the fat." This value-driven method prioritizes the actions that customers value. Everything else is waste and reduces efficiency and profits.
A good lean management system first defines customer value and all things that contribute to that value stream. Then, it eliminates activities that don't contribute to the value delivered by the body shop. Employees focus their efforts on worthwhile endeavors that improve the customer experience, and the company maintains its competitive advantage.
2. Adopt Advanced Scheduling Software
One of the best ways to retain customers is by making body shop services convenient, and that means easing the scheduling process while ensuring workflows that aren't impossible to maintain. Advanced scheduling software eliminates confusion regarding drop off dates and allows the company to organize large and small jobs to maximize production.
3. Streamline Repair Processes with Standard Operating Procedures
Scheduling is easier when body shops can predict their actions ahead of time. Of course, this isn't always possible. However, it can be accomplished for the most part when following standard operating procedures (SOPs). OEM repair standards exist for a reason, and if your staff has access to these best practices, they will repeatedly achieve safe and high-quality results.
4. Invest in Staff Training and Development
A body shop is only as good as its technicians, which is why investing in training and development is vital to the company's success. OEM certification is a stamp of approval that is sought by customers and insurance companies. It signifies that the body shop is equipped to handle the customer's vehicle at a standard that will benefit the customer.
5. Leverage Technology
Finally, a body shop should leverage technology to increase efficiency, quality, and convenience. Technology provides access to schedules, OEM repair recommendations, ADAS calibration, customer surveys, and a litany of valuable resources that will enhance the business.
Collision Resources is a software and consulting company that specializes in optimizing workflows in collision repair centers. To learn more about our scheduling software solutions or our body shop consulting services, contact us today!
Subscribe to Our Newsletter
Interested in receiving more tips delivered directly to your inbox?
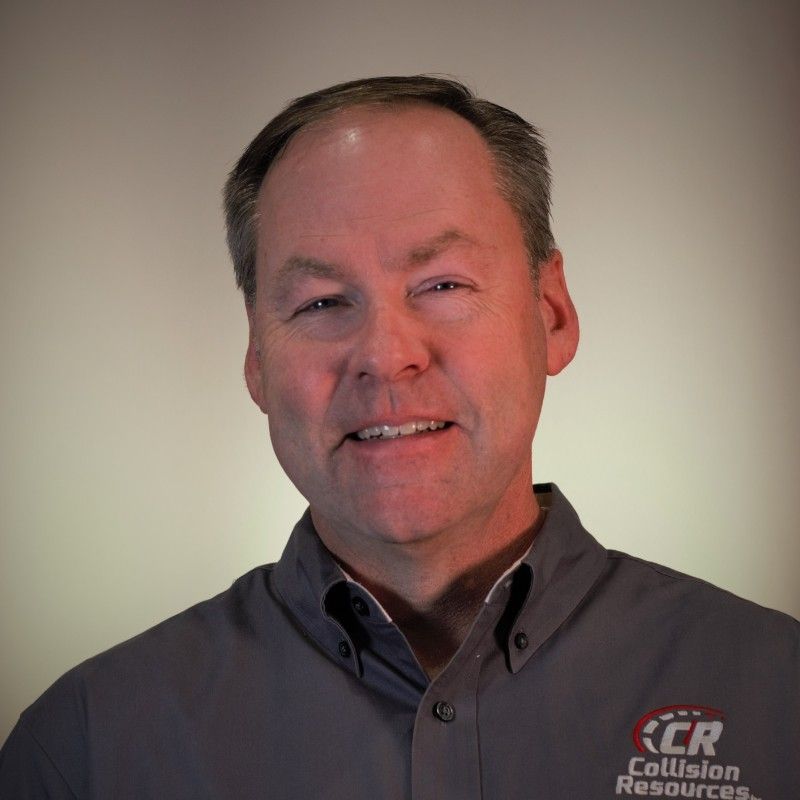
David McCreight is the Owner of Collision Resources and serves as President. Ultimately, David is categorically passionate about assisting auto body shop owners and managers to define and exceed their goals.